The need to improve industrial manufacturing processes to achieve higher productivity, obtain superior final products, and gain greater cost efficiency make the development of new materials practically essential, where coatings that improve the tribological, and even optical, properties of the substrate play a significant role. These coatings are applied to extend the service life and improve the performance of various products, including cutting tools, dies, and moulds, used in various sectors of industrial activity (transport, medical, metal forming, plastic injection, etc.)
Industrial sheet metal forming processes face various challenges, related to the durability of the dies and punches used. Some of the issues include thermal fatigue, contact fatigue, and wear and tear, all of which have a direct impact on process efficiency and the time spent maintaining these parts. These difficulties not only affect productivity, but also increase the costs associated with these operations. A solution can be found in the application of coatings, but the use of increasingly demanding and specialized materials limits the effectiveness of current coatings and conventional deposition techniques. Therefore, studying and developing new coatings is essential to address these challenges and improve the reliability of industrial sheet metal forming processes.
The PVD-MS (Magnetron Sputtering) technique stands out as one of the most studied methods to generate homogeneous coatings with precise control over composition and morphology. This makes it an especially valuable tool for adapted surface engineering. However, the need to improve industrial processes has led to the study and development of new coating deposition techniques, such as HiPIMS (High Power Impulse Magnetron Sputtering). Through this technique, and using new and more sophisticated structures such as nanocomposites and multilayer systems, coatings with improved properties can be achieved, such as higher density, better adhesion to the substrate, and greater hardness and mechanical properties, among others. This technique has been studied on a laboratory scale, but hardly at all on an industrial scale.
Within this context, Dr Neus Sala Bascompte conducted her doctoral thesis at the IQS School of Engineering, entitled Nanostructured ceramic coatings deposited by High-Power Impulse Magnetron Sputtering in an industrial scale reactor. Her thesis was jointly supervised by Dr Carles Colominas Guàrdia, from the Materials Engineering Group (GEMAT), and Dr Manuel D. Abad Roldán, from the Applied Mechanics and Advanced Manufacturing Group (GAM). It was conducted in collaboration with the company Flubetech, S.L., specialists in surface engineering innovation, the Institute of Materials Science (CSIC) in Seville, and Montanuniversität Leoben.
New ceramic coatings in reactors on an industrial scale
The thesis involved the design, deposition, and characterization of various nanostructured ceramic coatings using the HiPIMS technique in an industrial-scale reactor of the CC800/9 ML HiPIMS type by CemeCon AG at the Fluebetch, S.L. facilities. Dr Sala studied various coatings within her research:
- Incorporation of carbon into TiB2/TiBC coatings, resulting in the formation of TiBxCy ternary structures, which significantly improved the mechanical properties of the coatings.
- NbC/a-C(:H) coatings, with which a comparative study was carried out between the DC-MS and HiPIMS techniques, highlighting the need for a precise adjustment of the HiPIMS parameters to achieve coatings with superior microstructural and mechanical properties..
- Multilayer coatings of TiN/CrN, TiSiN/CrN, and NbN/CrN, whose properties were described in terms of deposition, microstructure, and composition parameters. In the case of these systems, exceptional hardnesses of the coatings was achieved, close to 32 GPa, due to phenomena that take place at the nanometre scale, with the formation of superlattice structures for coatings with bilayer periods of 15 nm.
The studies carried out in this thesis offer a comprehensive characterization of all the coatings studied, through the use of various techniques, as well as valuable perspectives on the potential and challenges of using HiPIMS technology in industrial reactors for the customization of advanced coatings that can respond to a wide range of industrial requirements and offer advanced solutions to current problems.
Related publications
N. Sala, M.D. Abad, J.C. Sanchez-Lopez, F. Crugeira, A. Ramos-Masana, C. Colominas, Influence of the carbon incorporation on the mechanical properties of TiB2 thin films prepared by HiPIMS, International Journal of Refractory Metals and Hard Materials, 107, 105884, 2022.
N. Sala, M.D. Abad, J.C. Sánchex-López, J. Caro, C. Colominas, Nb–C thin films prepared by DC-MS and HiPIMS: Synthesis, structure, and tribomechanical properties, Surface and Coatings Technology, 422, 1275690, 2021.
N. Sala, M.D. Abad, J.C. Sánchez-López, M. Cruz, J. Caro, C. Colominas, Tribological performance of Nb-C thin films prepared by DC and HiPIMS, Material Letters, 277, 128334, 2020.
This thesis has received funding from the Secretariat of Universities and Research with the Government of Catalonia’s Department of Business and Knowledge and European Social Funds [2019FI_B01190], [2020FI_B1_00114], [2021FI_B2_00167].
Colaborators
Research groups
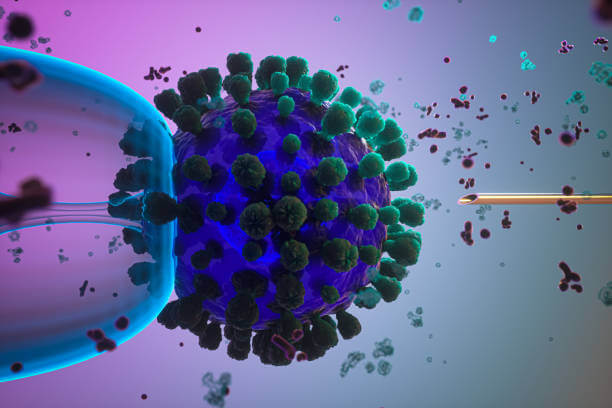
GEMAT – Materials Engineering
The GEMAT group (Materials Engineering Group) conducts its activity in three main areas: the development of new functional materials, surface engineering and biomaterials.
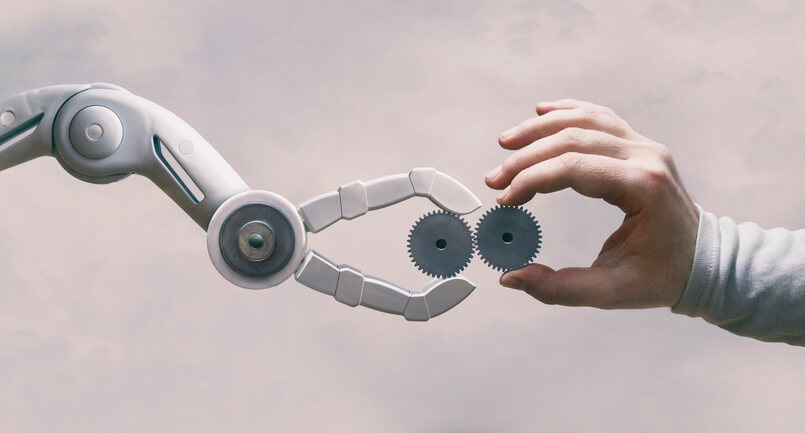
GAM – Applied Mechanics and Advanced Manufacturing
GAM (Group of Applied Mechanics and Advanced Manufacturing) is a multidisciplinary group of scientists and engineers focused on research and problem-solving related to the advanced manufacturing, the development, characterisation and efficient use of engineering-grade materials, and the enhancement of structural performance.